CamGuard
CamGuard is an FAA-approved additive supplement formulated to address the complex and interrelated problems of corrosion, wear, deposits and seal degradation in piston engines. CamGuard contains 11 high performance additives and is 100% active. It dramatically improves performance of and is compatible with all aviation oils including mineral based, and semi-synthetic types.
In addition to aircraft engines, CamGuard is extremely beneficial for corrosion control when added to the crankcase of any infrequently used engine. These include marine inboard and outboard engines, motorcycle, emergency equipment, backup generators, classic and antique vehicles, agricultural and all seasonal equipment. CamGuard is compatible with all passenger car and heavy-duty diesel oils. This includes synthetic motor oils.
What are the problems?
Corrosion
Corrosion is the destructive attack of a metal by chemical reaction with its environment. Rusting applies to the corrosion of iron or iron based alloys such as steel.
The presence of corrosion on the rubbing surfaces dramatically increase wear rates as the corrosion products are easily removed and often abrasive. In engines, corrosion manifests itself by causing material loss, surface property changes (pitting) and dimensional changes, dramatically increasing wear rates on critical steel components such as camshaft lobes, tappet surfaces and cylinder walls. It was this effect recognized by a major engine component re-conditioner that led to the development of CamGuard. Corrosion also attacks of non-ferrous metals and can damage bearings and bushings, degrade the efficiency of oil coolers and weaken structural components.
Wear
Wear is the gradual removal of material from one or both pieces of two materials that are in contact and moving relative to one another.
Engines have many parts found under such conditions including the interfaces of cam lobes and lifters, cylinders and piston rings and gears. Wear rates are determined by load pressures, relative speed, materials, surface properties and the lubricant. CamGuard anti-scuff and anti-wear chemistry protects engine components from startup to the highest possible temperatures.
Click here to see our latest wear testing results.
Deposits
Deposits are buildup of carbonaceous materials caused by oxidized fuel and lube products sticking to various engine components.
Deposits are the result of reactive precursors that attach to hot metal surfaces where they polymerize forming varnish and carbonaceous buildup. Deposits that limit or prevent the normal movement of components will increase wear rates dramatically. The oil additives must prevent oxidation of and disperse the reactive precursors for the life of the oil. Deposits once formed, for example on pistons, can causing rings to stick rapidly increases wear and may require the need for a premature top overhaul. CamGuard increases both the anti-oxidancy and dispersancy of the oil helping minimize deposit buildup as well as mitigate existing deposit problems.
Seals
Seals are synthetic rubber like materials that allow mechanical motion to occur outside the engine while keeping the oil inside the engine.
They seal the crankshaft while allowing it to turn both inside and outside the engine and their use allows access to many parts of the engine including valve covers and push rods. Over time and exposure to hot oil, seals may shrink and harden or they may soften and crumble. Neither is a pleasant prospect. The ability to protect from both scenarios can help minimize messy engine compartments and the need to replace seals before TBO.
CamGuard - The 5% Solution
* Turbocharged engine acceptance pending
Wear Testing
We performed wear testing of four oils and three additives was performed utilizing a FALEX Tribometer at a third party analytical laboratory. The FALEX PIN and V-block is a well-known tribometer that is used for many standardized lubricant tests. These include the ASTM (American Society for testing and Materials) D-2670 Standard Test Method for Measuring Wear Properties of Fluid Lubricants and ASTM D-3233 Standard Test Method for Measurement of Extreme Pressure (EP) Properties of Fluid Lubricants.
The test procedure utilized here is a derivative of the ASTM D-2670 and used by Phillips Petroleum and described in the Journal "WEAR" Volume 84, 1983. The Phillips test correlates very well with camshaft wear in automotive engines using gasoline engine oils. The loads in this testing were then reduced from the above reference and specifically selected to demonstrate effectiveness of the antiwear additives in commercial aviation oils. Aircraft engines were designed before there were antiwear oil additives. The engines were designed with wear surfaces hard enough and cam/ lifter and piston ring/ cylinder load pressures low enough that a film of heavy oil was enough to prevent excessive wear.
The test procedure consists of heating the test oil to 250 degrees F. and then with the pin rotating at 290 RPM slowly ramping up the load to 150 pounds and running for a three minutes break-in. The load was then stepped up to 250 pounds for 1 minute and then stepped up to 350 pounds. The total run time is 3.5 hours with a constant 350-pound load. The PIN and V- blocks are then cleaned and the total weight loss is measured and reported.
Ashless additives such as the triaryl phosphate ester functional fluids including tricresyl phosphate (TCP), butylated triphenyl phosphate (BTPP), and isopropylated triphenyl phosphate have historically been utilized as load carrying, plasticizers and flame-retardant additives in many applications. They are utilized extensively in turbine engine oils. These additives have never demonstrated useful performance in automotive applications i.e. the camshafts quickly fail. Automotive gasoline and diesel engines depend on the use of zinc diakyldithiophosphate "ZINC" for antiwear protection.
Like other bench tests, this is an accelerated test. The loads and initial temperatures of this test were specifically selected to test the antiwear capabilities of these oils and additives and not their extreme pressure (EP) properties, which occur at significantly higher loads. It is important to remember that even non-dispersant mineral oil passes the aviation certification test and consists only of basestock and antioxidant. The ashless dispersant (AD) non-antiwear additized oils have all successfully passed certification testing and it is important to note that this is a test to compare the antiwear additive chemistries under conditions just beyond those found in an engine. The test conditions were determined by using conditions that are just severe enough that the unadditized oils fail. Only after a great deal of testing under a wide variety of conditions was it determined that this procedure could be used to test the antiwear additive's effectiveness.
Figure 1 shows the results of tests at the selected conditions. The samples that did not make it up to the final load, 350 pounds, are shown as failing and marked accordingly. The samples that made it to the final load but did not run the full length of time, 3.5 hours, are shown as failing and marked accordingly. The W100 failed just before it reached the 350-pound final load and was chosen to be the reference for additive testing. The 20W-50 failed at 75 seconds but at a much lower starting temperature of 150 degrees F and could have been used as the reference as well.
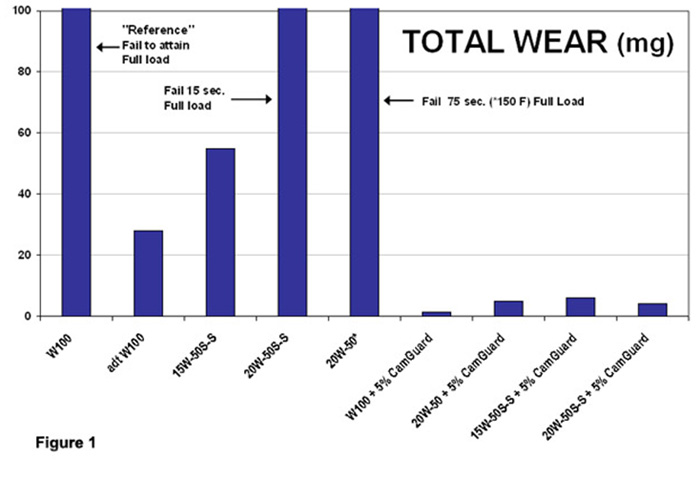
The addition of CamGuard to the reference W100 and 20W-50 shows excellent results as seen in Figure 1. W100 with CamGuard shows a very low 1.5mg while the 20W-50 with Camguard shows a very low 5mg.
The additized W100 Plus and the leading semi-synthetic (15W-50 SS) both of which claim antiwear protection performed well. The 15W-50 gave a total weight loss of 54.9mg and the W100 Plus gave a total weight loss of 28mg. The new semisynthetic 20W-50, which makes antiwear claims, failed 15 seconds after reaching the final load, in 5 seconds and 10 seconds in repeat tests. CamGuard was added to both of the semi synthetics the 15W-50 SS and 20W-50 SS and demonstrated excellent results with 6.1mg and 4 mg weight loss respectively also shown in Figure 1.
Additive A, a well know product, in W100 demonstrated no benefit over the W100 by itself as the sample failed to reach the final load. The metal parts, the oil and Additive A were heated and cooled multiple times per the manufacturer’s recommendations. Additive B, polymer resin, in the W100 sample made it to the final load but failed after 15 seconds. CamGuard in the reference W100 sample passed with a total weight loss of only 1.5-mg. The results are shown in Figure 2.
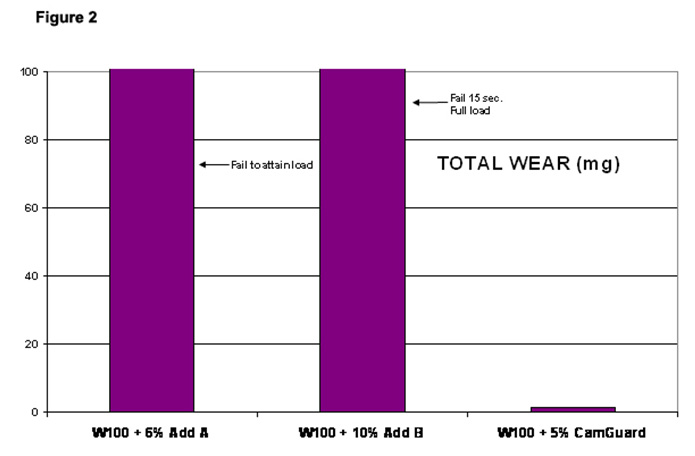
1) What is CamGuard and why do I need it?
CamGuard is a supplemental additive package for piston engine motor oils. It is a 100% active blend of 11 components and improves the performance of any oil in the areas of:
- Rust and corrosion protection
- Wear protection
- Deposit control
- Seal conditioning
CamGuard offers an advanced level of protection to every engine. Infrequently used engines will see the most benefit as rust and corrosion dramatically reduces engine life.
2) Will CamGuard work with any oil?
CamGuard works with all conventional mineral oils, semi-synthetic oils, and fully synthetic oils. It is compatible with all commonly used oil components including detergents, dispersants, zinc or phosphorus antiwear compounds, antioxidants, friction modifiers, basestocks, etc.
3) Can I use CamGuard in other engines?
CamGuard is useful in ALL engines. Infrequently used engines will be the greatest benefactors.
4) Is CamGuard like any other additives?
NO! CamGuard is a complex formulation using proven additive technology. It is not just an additive diluted in baseoil and backed up with a slick marketing campaign or some historic mystical potion.
We present our data from both industry-standardized tests and in house testing along with our experimental procedures for comparison and evaluation.
5) Do I need to add CamGuard at every oil change?
Yes. We do not make claims of one-time engine treatments.
6) Can I use CamGuard in a high time engine?
Yes, CamGuard is valuable at any point in an engines life. When added to a high time engine, oil analysis will often show an increase in metals across the board for a few oil changes. CamGuard does not clean engines but does allow them to clean themselves. This is reflected in both an increase in lead and insolubles levels. Lead levels may double as oil flow disperses deposit precursors for the next few oil changes. The increase in other metals is seen going up and is artificial as is the lead. If lead is twice normal then divide the other metal numbers by two to get the values for those metals.
An increase in the insolubles is a function the mechanical motions of the rings and valves cleaning up the ring grooves and valve guides.
7) What differences can I expect to see when I use CamGuard?
CamGuard is a prevention product; it reduces wear, corrosion, deposits and seal degradation. Regular oil analysis typically demonstrates a trend of reduced iron levels when using CamGuard. Iron levels are reduced due to both rust inhibition and wear protection. Reduced levels of copper, lead and tin are often reported due to better corrosion protection. Silicon levels are often reduced demonstrating protection of silicone gaskets and O-rings. Note that there are trace amounts of calcium (20-25 PPM) when the correct amount of CamGuard is used.
8) How often should I change my oil?
In aircraft, we recommend 25-30 hours with a minimum of four times per year using 5% CamGuard with each oil change. If the engine will sit idle for any length of time, we recommend fresh oil and 5% CamGuard. Be sure to run the engine to circulate the clean oil and check for leaks before letting the aircraft sit.
For boats follow the manufacturer recommendations for oil changes and add 5% CamGuard to prevent wear, valve-train or cylinder rusting. Before storing your boat always change your oil, add CamGuard and run the engine to circulate the clean oil.
9) Is CamGuard helpful as a long-term preservative?
CamGuard can be used as a pickling or preservative oil at a concentration 7-8% in fresh oil. Be sure to run the engine with the fresh oil and CamGuard to circulate and follow any other manufacturer’s recommendations for long-term storage.
10) Does CamGuard treat the metal?
The additives in CamGuard react with various metals in the engine. Corrosion inhibitors form a continuous layer on soft metals blocking water and preventing acidic attack. Ferrous metal corrosion inhibitors do the same thing on iron and steel even as the oil runs off hot parts after engine shutdown. Some anti-wear components form sacrificial antiwear films at cam lifter interfaces, while others prevent wear of dissimilar metals such as valve / guide interfaces.
11) Will CamGuard reduce my oil consumption?
It may, but it entirely depends on the reason for the increase in consumption. If the rings or the valve guides are worn then you will not see any decease in oil consumption. However, if your oil consumption has recently increased and is caused by ring belt deposits, then the use of CamGuard will help free up sticky rings and return consumption and performance back to normal.
12) Will CamGuard reduce my oil or cylinder head temps?
It may, but probably not. CamGuard is not specifically designed as a highly friction modifying additive package out of concern for certain friction fit engine systems i.e. Continental engine starter adapters. Some of the components in CamGuard offer friction reduction in lightly loaded parts and may improve fuel economy.
CamGuard - The 5% Solution
* Turbocharged engine acceptance pending